Vacuum Forming
Introduction
It's time to re-engineer the traditional method...
Vacuum forming is a manufacturing process by which a sheet of plastic is heated and pressed over a form to create a part. This process is used to create many of the products in your home such as plastic containers, tubs, sink units, and electrical enclosures. 3D printing is a great way for manufacturers to create low cost molds for low volume manufacturing or prototyping. While we used an industrial vacuum forming machine to achieve our application, you can also build one at home to achieve the same effect.While working time will vary, this process took us about 1 hour from start to finish. Thermoforming is a manufacturing process used to shape thin sheets of thermoplastics common in the packaging, medical, industrial design, and automotive industries. A wide variety of everyday items are created using thermoforming, from takeout containers to RC cars. Vacuum forming is a type of thermoforming that uses thin sheets of special plastic and a vacuum. Heat makes the plastic pliable, and then vacuum is used to pull the heated plastic sheet around the mold. Typically molds are made from wood, cast aluminum, machined aluminum, or composites. Using these materials can be costly and time consuming.
Many companies are turning to 3D printed molds for this application. 3D printing the molds is allowing thermoformers to do iterative sampling and even custom forming for their customers at a low cost and high speed. Parts created with a printed mold can be used at any stage of product development, including production, concept development, and prototyping phases.
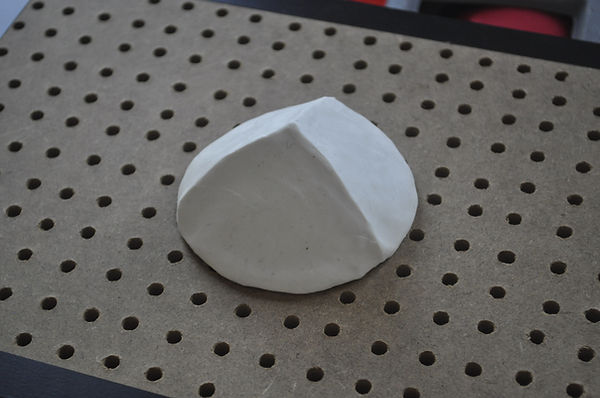
Process flow chart

Benefits
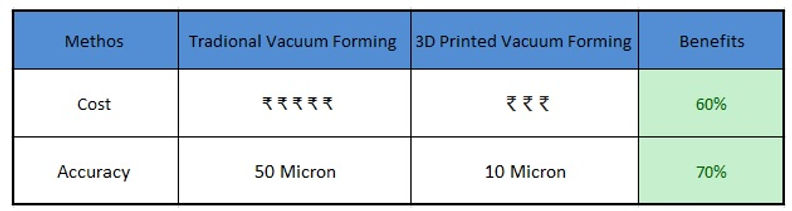
Images

Vacuum Form Part
3D Printed Part