Now Investment #Cast your #3DPrints
- Vishal R. Jariwala
- Apr 30, 2017
- 3 min read

Why 3D Printing???
For prototypes and short production runs, creating wax patterns from 3D printed molds offers substantial time and cost savings over traditional tooling methods. Plus, 3D printing can produce molds with greater complexity without driving up costs.
Introduction
It's time to re-engineer the traditional casting
Investment casting, also called lost wax casting, is a process in which a pattern, also known as a master or master pattern, traditionally made of wax, is covered with a ceramic slurry. The wax pattern is normally produced with injection molding.It is generally used in applications that have relatively low production quantities and changing product designs.
The wax patterns used in investment casting are typically produced using an injection molding process. Tooling cost ranges from1 Lakh to 25 Lakh and lead time to produce tooling is approximately two months. A big problem for many investment casting foundries is that they are not able to produce prototype castings until the injection mold is completed. At this time, problems are often discovered, such as interference with other components in an assembly. Additional time and money must be invested to fix the injection mold. In a worst-case scenario, it may be necessary to scrap the original tool and start over from scratch. Another problem with wax patterns is that their complexity is limited by what is feasible from an injection mold in the allotted time.
Fused Deposition Modeling (FDM) provides an alternative method for producing investment casting patterns that can provide dramatic time and cost savings. FDM technology is an additive manufacturing process that builds plastic parts layer by layer, using data from CAD files. FDM makes it possible for the foundry to produce a pattern that can also serve as a prototype for form and fit evaluation. In one day, the foundry can provide the customer with a prototype that provides a perfect match to the casting that would be produced if it becomes the pattern. The strength of the materials used in the FDM process makes it possible to put the FDM component into an assembly and perform testing. If any problems are discovered, the foundry can usually make the changes requested by the customer and build a new pattern in about 24 hours.
As soon as the customer approves the prototype, the foundry can move into production by using the FDM parts as patterns for investment casting. Since FDM is an additive process, the pattern can be as complex as needed without any impact on cost. (With injection molding increasing pattern complexity often requires a more complex and more expensive tool).
Other advantages of FDM patterns are that they have greater strength, toughness and accuracy than wax or other additive manufacturing technologies. This durability is important because it prevents damage that often occurs in the transportation and handling of patterns made of wax or other materials.
How to Implement???
FDM patterns are direct replacements for traditional patterns that are injection molded with foundry wax. One significant difference is that FDM material does not melt like wax. It burns, which leaves a small amount of ash, typically 0.021 percent, in the shell cavity. The ash is later removed in a shell washing operation. Venting should be added to the ceramic shells to speed the burnout of the FDM pattern. Investment casting patterns need to be produced to close tolerances and with an excellent surface finish because any defects are reproduced in the finished part. J Group Finishing Touch Smoothing Station uses a semi-automated process to improve the surface finish of FDM parts to near injection molded quality without the labor or cost associated with traditional finishing. Advancements in finishing technology have improved FDM parts to the point that hand finishing is no longer needed, making FDM a much stronger competitor in the investment casting market.
Process Flow Chart
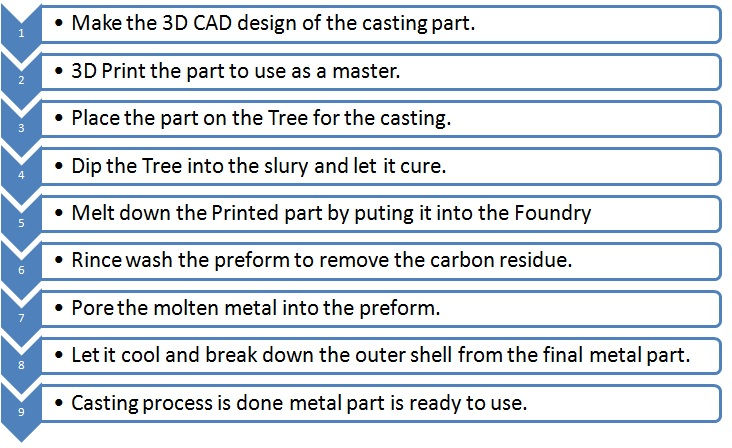
Benefits

Case Studies


Comments